LB-762 Mushroom-Growing Cellar Climate Regulator - Upgrades, Innovations, Implementations, Ideas
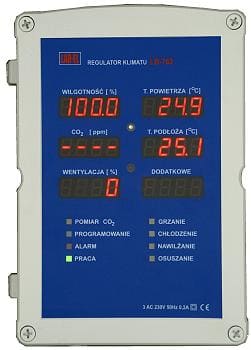
- Working with the following operating systems: XP, Windows 7, Windows 8, Windows 10
- New version of measuring probes
- Additional
LB-762-IO extension module
- New software functionalities:
- different ways of controlling humidity, based on:
- two-stage temperature regulation
- explanation
of alarms and exceptions
- extension of settings from remote control in LB-762
- thawing phase
- oxygen measurement
- overpressure measurement
- additional
measurements in boiler-room, chiller, cold storage
- corrections of reported errors
- Mushroom-growing cellar software
- Operation via
portable tablet in mushroom-growing cellar
- Software update
- History of changes in LBX software
- History of changes in LB-762 regulator software
- Configuration of regulators
- Selection of PID coefficients for regulation
- Reporting remarks about the software
Update of measuring probes
Current design of measuring probes ensures stable measurement results. In order to differentiate them, the new psychrometric sensors and probes for substrate temperature and air-conditioning feature colour-coded leads, thus they should be connected to the regulator’s boards as shown in the figure. Particular attention should be exercised in order not to reverse the terminals of temperature probes (T and GND terminals).
Updates, new implementations, new ideas
Subsequent
implementations of new features may be tracked in the archive and in
the history of changes of the SCADA LBX software and internal
software of the LB-762 regulators.
LBX software changes described below pertain to version 2.4 of the LBX PC software or later and version 1.14.1 of the internal software of LB-762 controllers (firmware) or later.
REMARK 1: From version 2.x onwards, compatibility between different versions of servers and LBX software clients is not supported, which means that the installation of the same (e.g. 2.2) version of the LBX software both on the main computer (on LBX server), as well as on the other computers operating within common system (on LBX client computers) is required. If, for example, the server uses version 2.2, and the client 1.7.87, it will be impossible to establish communication between the client and the server of the LBX software.
REMARK 2: In order to boost the system’s speed and efficiency, for establishing connection between LB-762 regulators with the LBX server it is recommended to use Ethernet interface (as a standard, 4 x 2 wires in a shield), instead of the old-type RS-485 interface (2 wires per shield).
Anemometer — measurement of air flow speed in a cellar area
The LB-762 regulator has been expanded to include the LB-762-IO module with additional interfaces: measurement inputs (including 4 for anemometric probes) and additional control outputs. Details are given in a separate description.
Controlling humidity in a number of ways
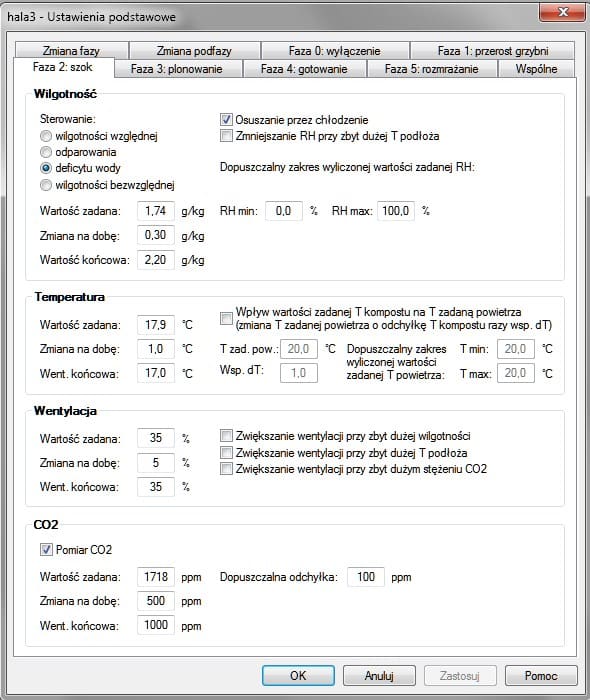
Accordingly to the adopted technology of mushroom-growing, it is useful to employ the right means of measurements and air humidity regulation in a mushroom-growing cellar. The Mollier graph or the LAB-EL Humidity Calculator software (available also for smartphones and tablets) may be used for calculating between different units that describe air humidity and for showing their temperature dependence.
Control based on relative humidity — current
LB-762 regulator monitors the current humidity in a cellar and by controlling the humidification and dehumidification it delivers the desired level of humidity in the cellar. This is the basic and most widely used means of regulation. Relative air humidity is temperature dependent.
Controlling based on relative humidity — estimated
Since the relative air humidity is temperature dependant, trying to obtain humidity equal to the current value before the temperature has stabilized, may lead to pointless humidity changes and energy losses. Control based on an estimated humidity facilitates the reduction of such losses. To this end, the LB-762 regulator calculates the actual and the desired absolute humidity (actual on the basis of the actual temperature and relative humidity, based on the temperature and the desired humidity), and the regulation process is performed on the basis of the target absolute humidity. The above graph shows the way in which the air parameters change between the points marked in blue: the change in temperature with constant relative humidity retained. The red path — maintaining a stable relative humidity with the use of continuous regulation; the red path — change in humidity on the basis of absolute humidity indication on a target point. As it can be seen, the green path is more optimal due to the uniformity of absolute humidity changes — it is shorter and thus it requires less energy.
Controlling based on relative humidity — estimated, is enabled in Equipment settings — air-conditioning.
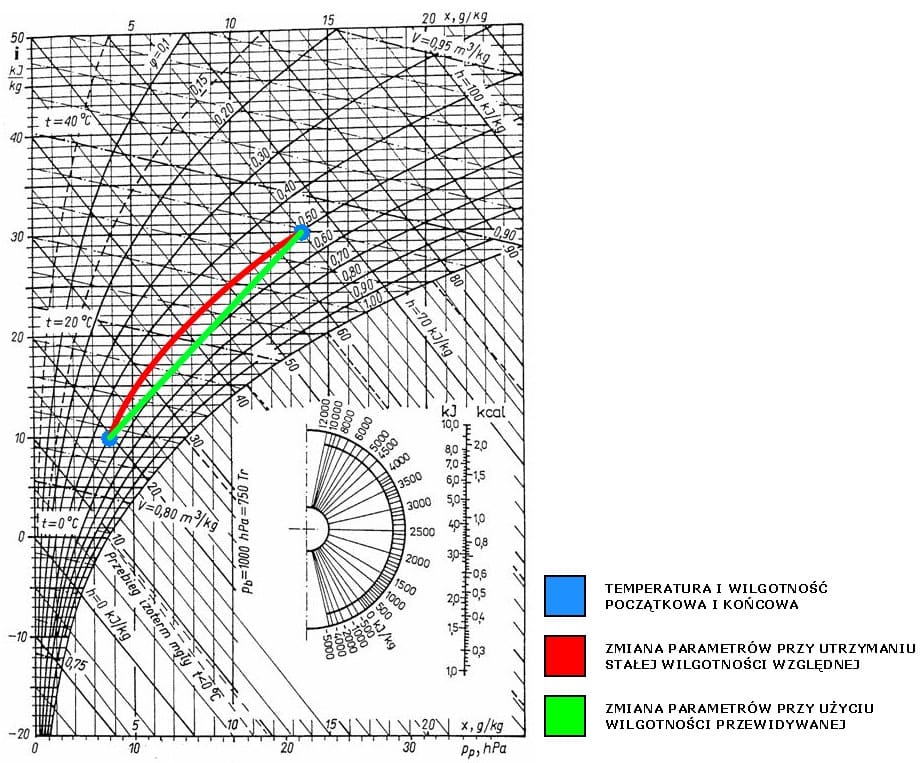

Control based on evaporation
This method is used for maintaining a level of humidity in the cellar so that the cultivated mushrooms evaporate a constant amount of water, indicated in g/h (grams per hour). In order for the regulator to set evaporation from the cultivation (that is how much humidity the cultivated mushroom evaporates), it is necessary to establish many additional parameters:
- air humidity and temperature in the cellar;
- air speed in the inlet with the actual ventilation speed;
- cross-section of the air inlet, which — together with the speed — enables the volume of air coming into the cellar to be calculated;
- air humidity and temperature in the inlet — an additional wet-and-dry bulb thermometer installed in the outlet of the climatic tunnel is required;
- estimated vaporisation efficiency — the proportion of humidity drawn into the cellar, as an outcome of humidification, that actually ends up in the air in the form of water vapour (the rest escapes in the form of a water running down the walls/floor).
The above parameters allow the absolute humidity in a cellar and in the outlet to be calculated. The difference between the two quantities is the water mass that appears in the form of cultivation evaporation.
The adoption of this method requires another wet-and-dry bulb thermometer, located at the air outlet of the air-conditioner.
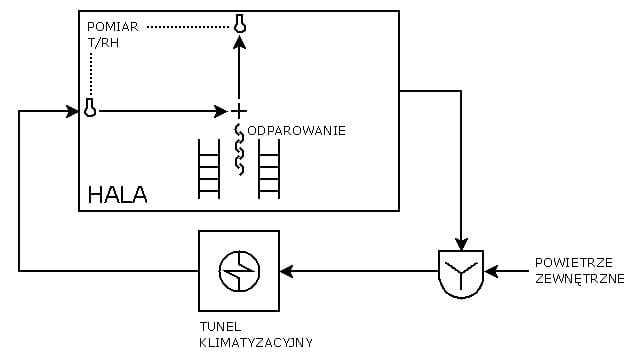
Control based on water deficit
Water deficit indicated in g/kg (grams of water per one kilogram of dry air) is a method for determining humidity — that is, how much humidity (absolute humidity) is missing to fully saturate the water humidity (that is until the relative humidity equals100%).
As it can been seen in the adjacent chart, where the blue sections mark the constant water deficit = 2 g/kg (as an interval between the red line marking full water vapour saturation and at the same time the relative humidity = 100%), the constant value of humidity defined this way means different relative humidity in different temperatures.
The air water deficit value is temperature dependent.

Control based on water content — absolute humidity
Water content in g/kg (grams of water per kilogram of dry air) is a method for the determination of humidity, based on the determination of absolute humidity mass for a specified mass of dry air. Water content is a unit of absolute humidity that is not air temperature dependent.
In the previous chart the green section marks an exemplary value of absolute humidity = 11 g/kg.
Two-stage temperature regulation
Two-stage temperature regulation is a more advanced form of regulation that may provide better results. In this process there are two interconnected regulation mechanisms, implemented in the LB-762 regulator:- The first stage — the cellar parameters: on the
basis of the current temperature measured in the cellar and the set
temperature, the regulator calculates the temperature set at the outlet
of the climatic tunnel, and this temperature is then used as the set
value for the second stage of the regulation.
- The second stage — air-conditioning parameters:on
the basis of the temperature set in the first stage and the temperature
measurement in the climatic tunnel, the regulator determines how to
control the working equipment: heating and cooling.
Two-stage regulation allows smaller variations of air in the cellar to be achieved. The first stage of regulation sets a relatively slowly-changing desired air-conditioning temperature, and the second stage of regulation delivers the set parameters in the climatic tunnel, which in turn may occur much faster, more efficiently and with lower parameter variations and smaller changes in the efficiency of the working equipment.
In the case of single-stage regulation, the thermal inertia of the cellar is very high and the reaction time to changes in heating and cooling is also very long. In the case of two-stage regulation, the thermal inertia of the regulatory system in the climatic tunnel is much lower, the working equipment functions more smoothly, and a separate regulatory section, with no direct influence on the working equipment, is responsible for setting the right temperature at the outlet of the air-conditioner — the temperature that will trigger the correct air parameters in the cellar.
It is recommended to enable the two-stage temperature regulation in the tab: Advanced settings — temperature regulation.
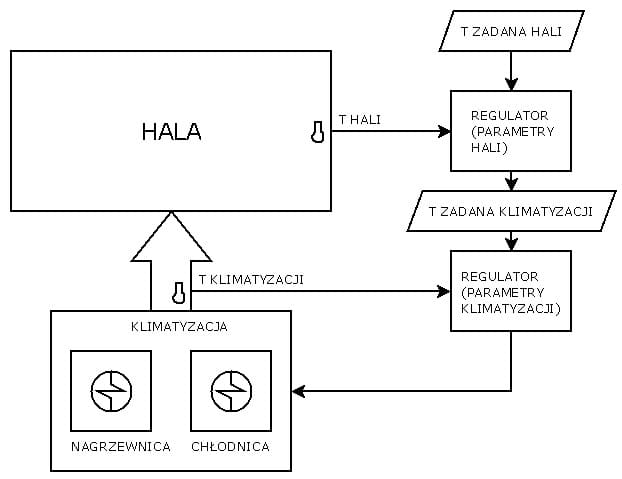
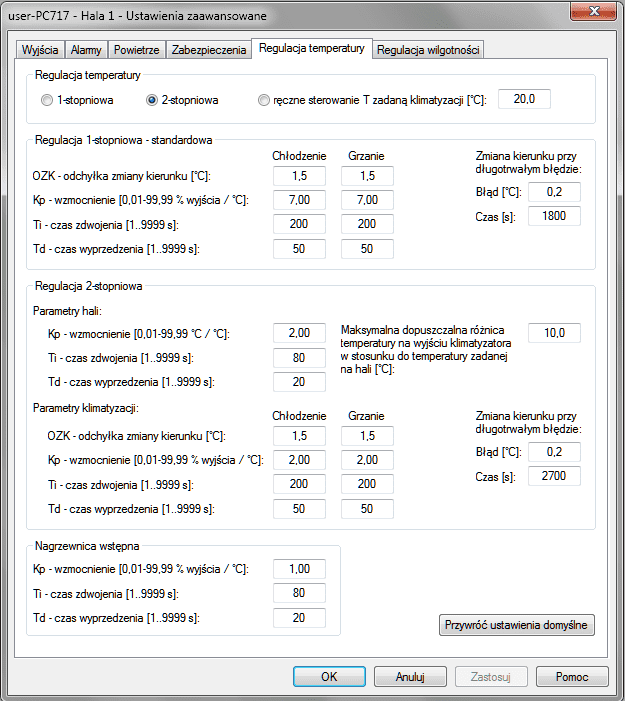
Explanation of alarms and exceptions
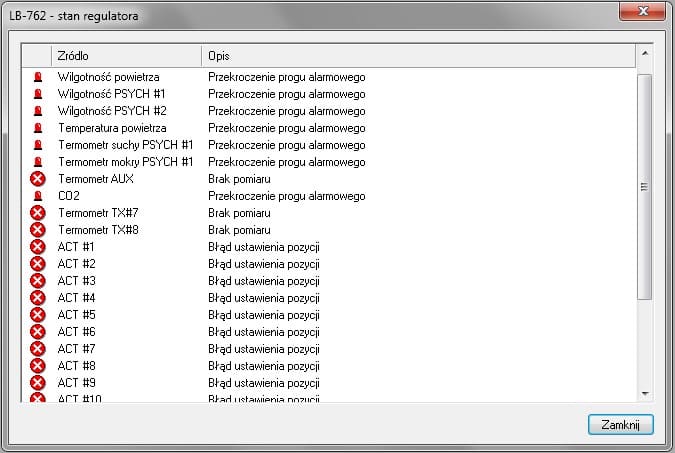
Complex regulatory procedures and a large number of interdependencies may result in a vague evaluation of the condition of the LB-762 regulator. In order to avoid this, an additional function is implemented to display alarms and exceptions noted by the regulator’s software; a dedicated screen in the LBX software is used to this end. In the adjacent example, states of alarm are triggered when the upper and lower value thresholds are exceeded, the absence of some measurements and the absence of a return signal from the servos are all visible. In practice, the screen enables the rapid diagnosis of system malfunctions and diagnosis of its behaviour.
Remote control settings in LB-762 regulators
With the use of the LB-765 remote controller, it is possible to set the operating parameters of LB-762 regulators (like in the case of LB-760A regulators). The programming of individual parameters (their sets) is stage dependent — it will differ slightly at each stage. Detailed operating instructions on how to use the regulator with the remote control is provided in the User Instructions.
Additional “Thawing” phase
In the LB-762 software, an additional Thawing phase is added for usage in the winter period to thaw frozen blocks. The whole machinery is then switched off, except for the heater, which is controlled in order to obtain the desired temperature in the cellar. Ventilation and air inlet openings are set to a constant value.
Oxygen content measurement
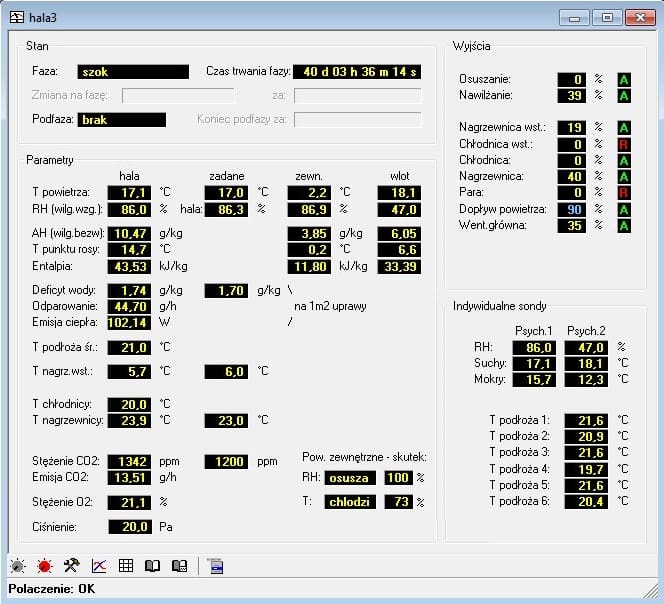
Additionally, oxygen content measurement is available for mushroom-growing cellars. It is also possible to regulate the fresh air inlet, based on CO2 (carbon dioxide) measurement (the same as previously) or on the basis of O2 (oxygen) concentration. To this end, in the CO2 measurement box an additional LB-905 oxygen concentration meter in a flux casing must be installed. The same air that passes the existing CO2 concentration meter, passes the new meter. The digital input signal from the O2 (oxygen) meter is connected to the S300 input from the same LB-762 regulator, to which the CO2 (carbon dioxide) meter is connected.
Overpressure measurement
Additionally, overpressure measurement is available for the mushroom-growing cellar. For this, an additional LB-716AD1 differential manometer must be installed in the cellar. The digital input signal from the manometer is connected to the S300 input of the LB-762 regulator; both the regulator and the manometer must be installed for the same cellar.
Additional measurements for boiler-rooms, chillers, cold storage, etc.
Contemporary mushroom-growing cellars are not just growing cellars, but also a boiler-room generating technological heat, a chiller generating technological cold, and a cold storage to store harvested mushrooms. Every additional room features working machinery — any malfunction translates into considerable financial losses. For this reason it is necessary to permanently monitor the temperatures at critical points, e.g.: the temperature of hot water from the stove, the temperature of water from the chiller and the temperature in the cold storage.
All additional measurements that the technologist may consider to be important, may be measured with additional thermometers and displayed in the very same LBX software, in which the measurement results from the growing cellars are displayed. For all additional measurements, the alarm thresholds may be set in the LBX software in order to signal the occurrence of any malfunctions. Depending on the temperature range and the required accuracy, an LB-489 hub (with 4 inputs) or an LB-480 hub (with 8 inputs) may be used, together with TN type sensors, e.g. substrate thermometers to LB-762. If greater accuracy is required, LB-710TX converters with the Pt1000 type sensors should be used.
Moreover, the LB-480 hubs are equipped with configurable measurement inputs that as well as enabling all LAB-EL sensors to be connected also ensure compatibility with different sensors from other manufacturers, e.g. manometers with 4…20 mA output, sensors with NO/NC output (e.g. door opening, alarm output for aggregate unit malfunction, three-phase power failure), etc.
The hub connects with the LBX server via an Ethernet, and the thermometers and other sensors are connected to the hubs. The LBX software may require a licence extension for additional measurement capabilities.
Corrections of reported errors
In the SCADA LBX software and internal software of the LB-762 regulator a number of reported issues have been fixed:
- the display of calibration coefficients;
- the calculation of CO2, heat and evaporation emissions;
- regulatory procedures;
- the flap closing after a power failure.
Reporting remarks about the software, assistance in configuring the regulator
All questions and remarks concerning the functioning of the LBX
software that operates the controls in mushroom-growing cellars,
suggestions for further development of the LBX software and user
experience issues as well as their requirements for growing should be
reported to
We provide free-of-charge assistance in the correct configuration of mushroom-growing cellar regulators. For this reason it is necessary to establish an Internet connection for a given mushroom-growing cellar, so that we — with a phone call — are able to observe the regulators’ functioning (charts) and correct their settings. Feel free to phone us for more details.